No dobra, trzecią stronę zaczynamy od zaskoczenia. Poprzednio skończyliśmy na włożonymcałym okładzie korbowo-tłokowym, a teraz mamy pusty blok?!? Tak.
Okazało się, że znalazłem niechcący błąd w katalogach. Tłoki nadwymiarowe, które kupiłem, miały mniejszą wysokość kompresyjną (jest to odległość od osi sworznia tłoka do denka tłoka). Nadawałyby się idealnie pod turbo, ale niestety ten silnik nie będzie miał turbo :). Wysokość kompresyjna była mniejsza o ~2mm, co powodowałoby obniżenie stopnia sprężania. Nie podobało mi się to.
Próbowałem wymyślić kilka rozwiązań, jak np. planowanie bloku, wymiana wału korbowego na taki od 2.9 (ma większy skok)... niestety żaden z tych pomysłów nie sprawdziłby się w praktyce. Dlatego ze spuszczoną głową znalazłem w stercie swoich części tłoki nominalne w idealnym stanie (właściwie nowe), chomikowane na jakąś okazję kiedyś, a następnie oddałem blok do tulejowania cylindrów pod te nominalne tłoki.
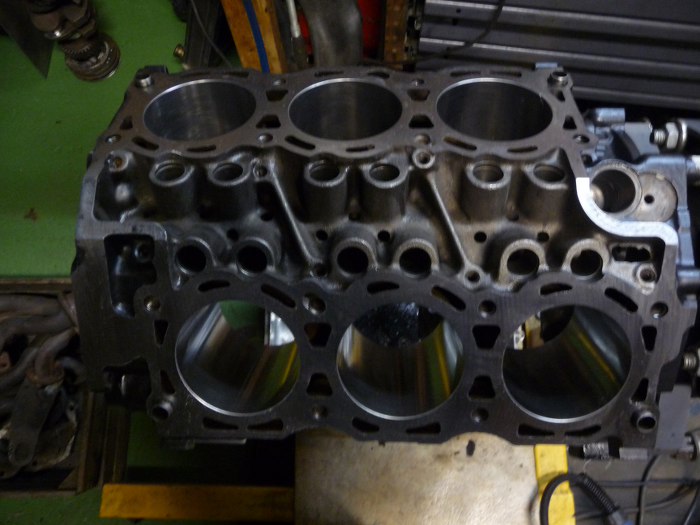
Wał został doważony pod tłoki, które będą teraz użyte. Po włożeniu panewek i posmarowaniu ich olejem położyłem wał korbowy na miejsce. Następnie założyłem uszczelniacz tylny wału - najłatwiej to zrobić w tym momencie.
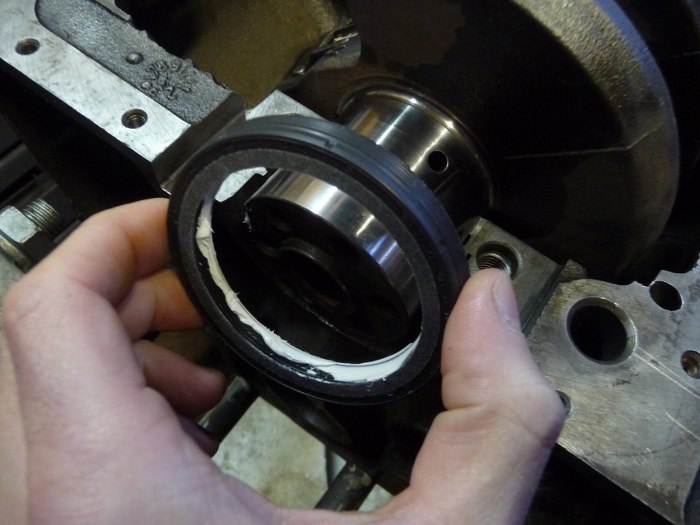
Gotowe do przykręcenia stóp wału.
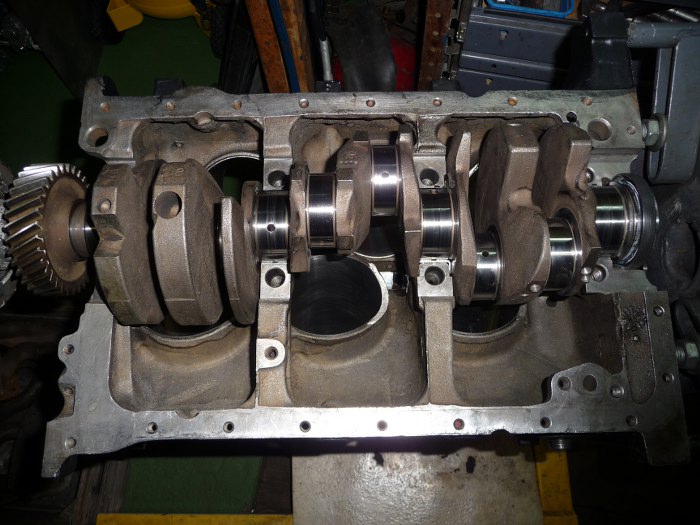
Musiałem jeszcze tylko przygotować czwartą śrubę pod blachę w misce olejowej.
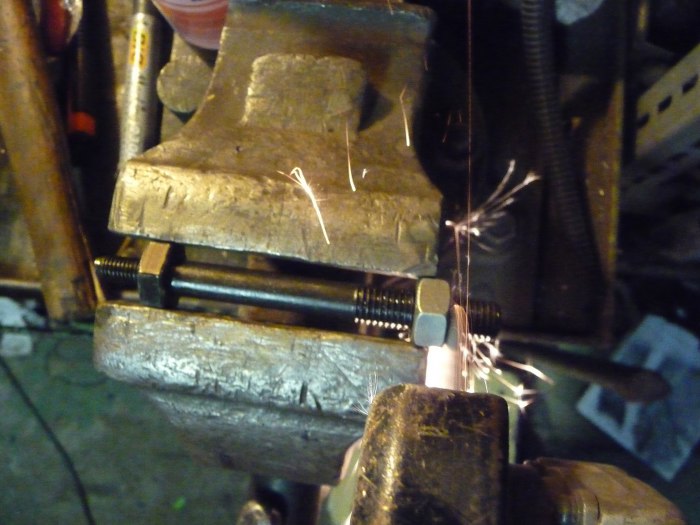
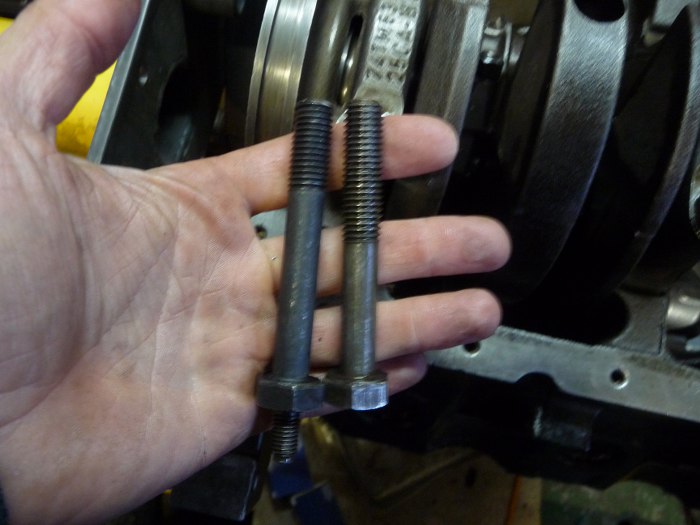
Przykręcone.
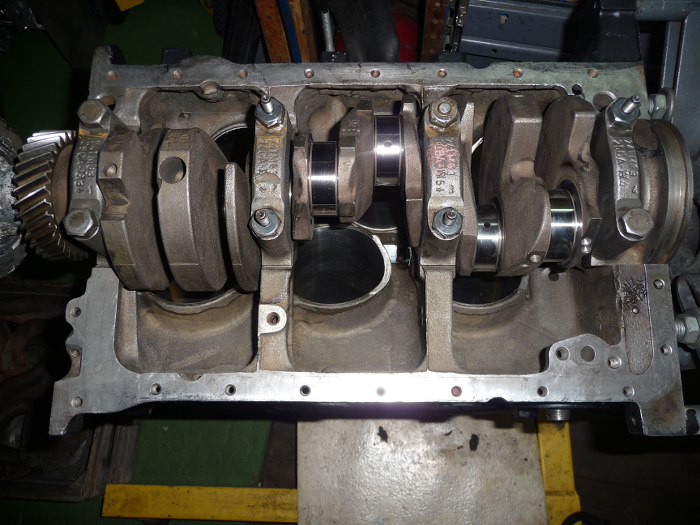
Następnie dokupiłem brakujące obecnie pierścienie. Poprzednie były do nadwymiarowych tłoków.
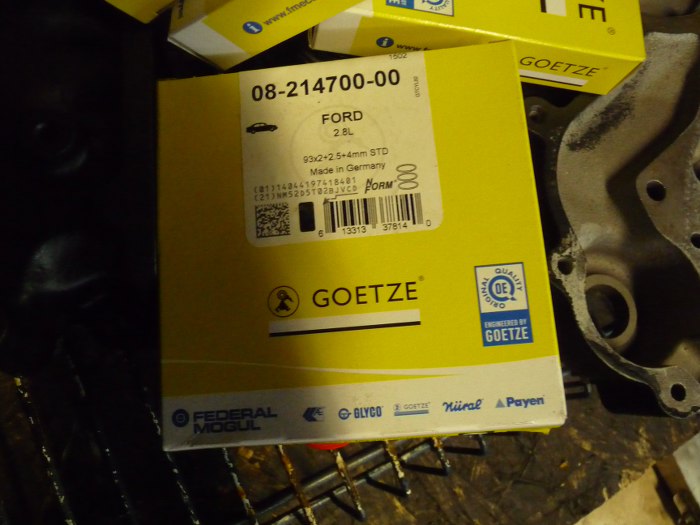
Wreszcie się nauczyłem korzystać z przyrządu do zakładania pierścieni! Jakoś nigdy do niego nie miałem serca, wolałem robić to ręcznie, ale już mnie palce od tych pierścieni bolały :)
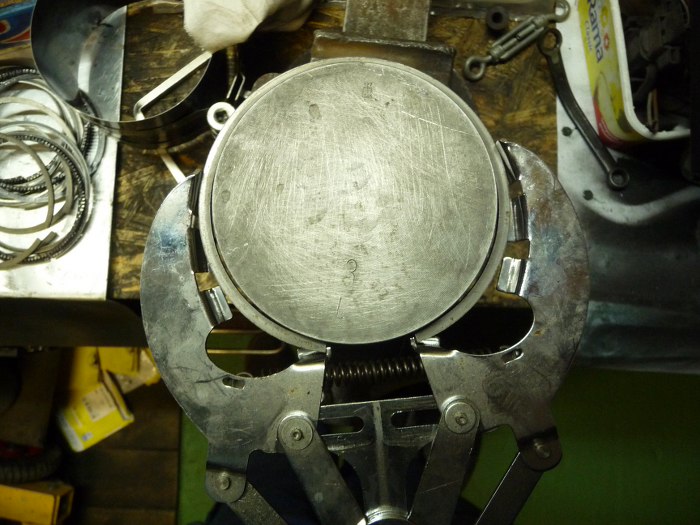
Następnie standardowo - ściśnięcie pierścieni i założenie osłonek na śruby korbowodu, żeby nie uszkodzić wału.
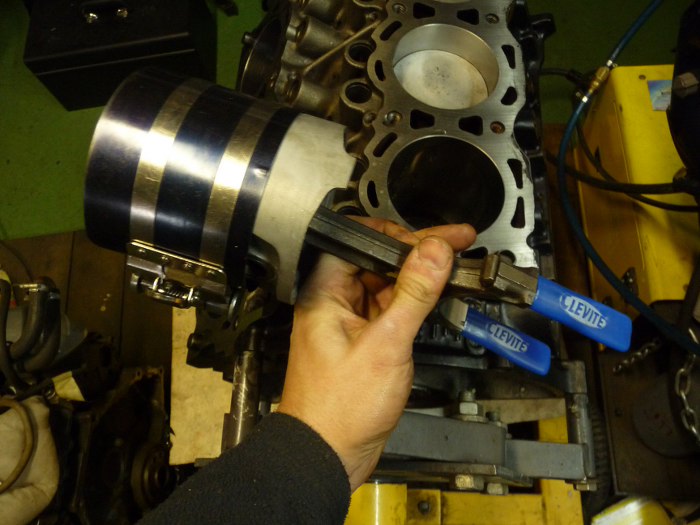
Po włożeniu każdego z tłoków warto zrobić z 2-3 obroty wałem korbowym, żeby sprawdzić, czy wszystko obraca się bez dziwnych oporów.
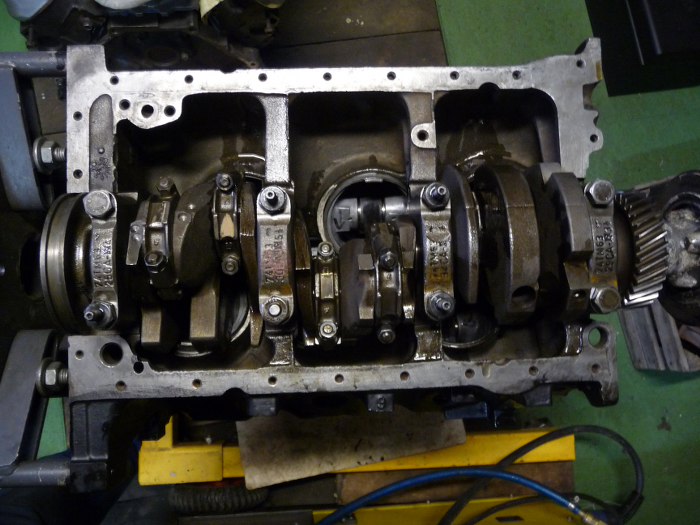
Następnie przykręciłem blachę na stopy wału.
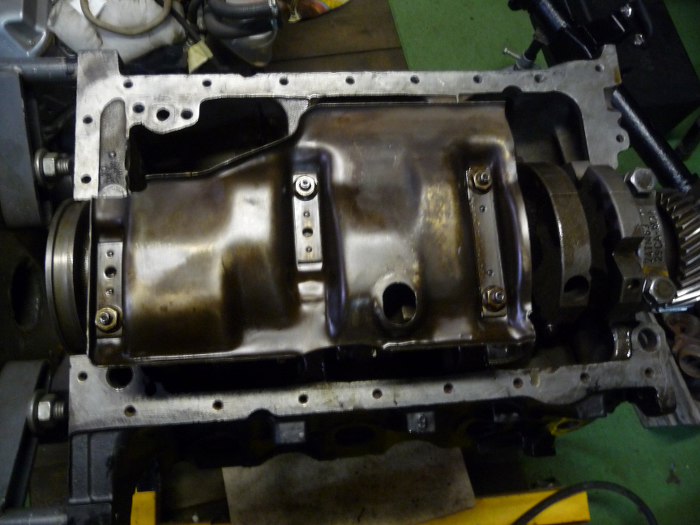
Tak to wygląda z góry. Teraz jest ok, bo tłok w górnym położeniu jest na równo z płaszczyzną bloku, a poprzednie tłoki były ~2mm poniżej tej płaszczyzny.
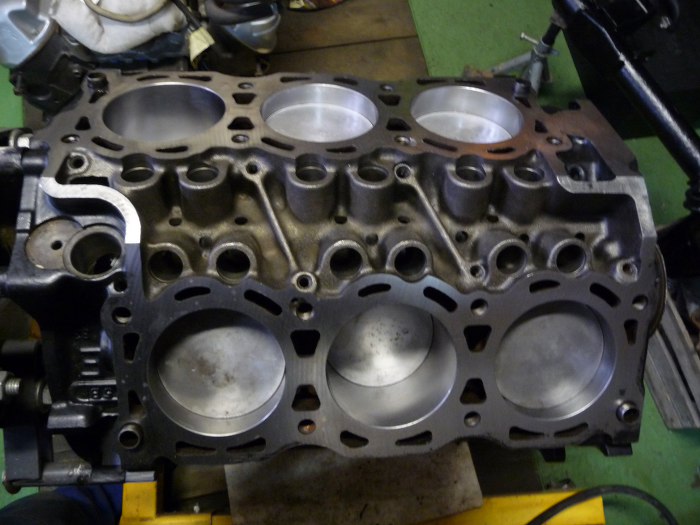
Następnie wziąłem się za to, na czym skończyłem poprzednią stronę - za szukanie brakujących elementów mocujących. Znalazłem 3 :)
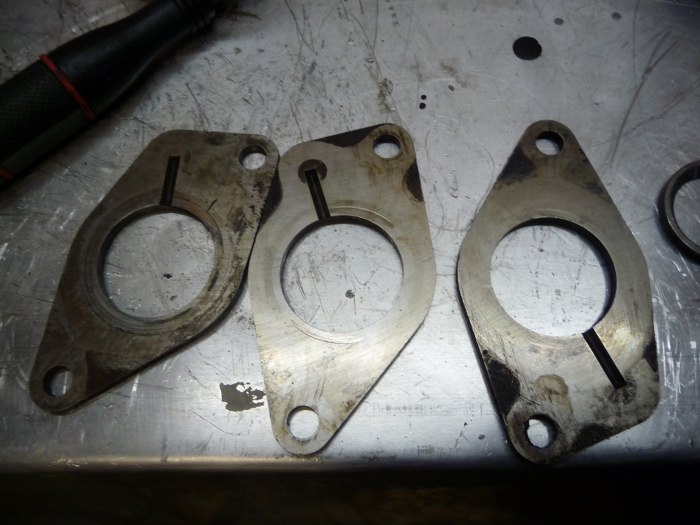
Po wybraniu najlepszego, poszukałem jeszcze śrub, klina i podkładki dystansowej.
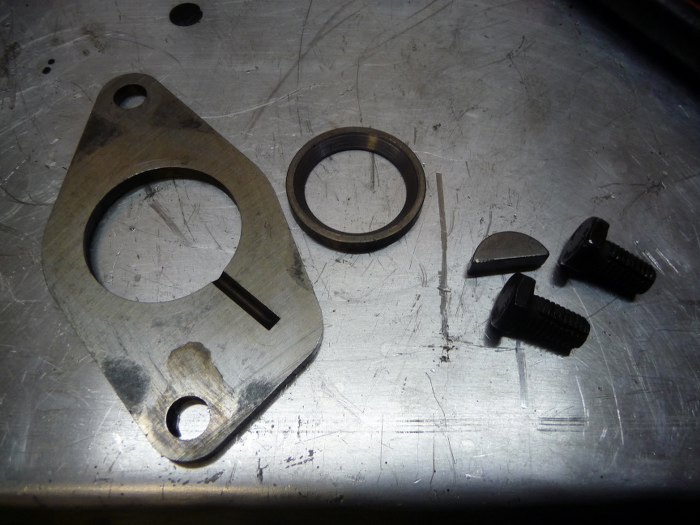
Podkładkę trzeba założyć podtoczoną stroną w kierunku wałka rozrządu.
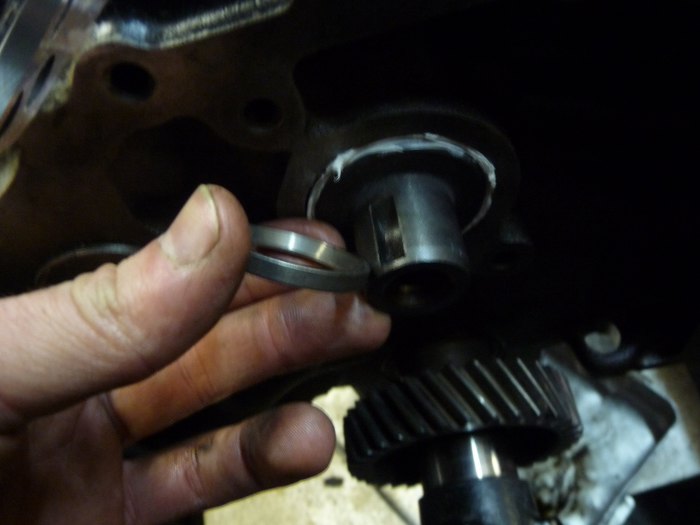
Następnie musiałem wykombinować jak wcisnąć klin w wałek. Stanęło na kluczu francuskim.
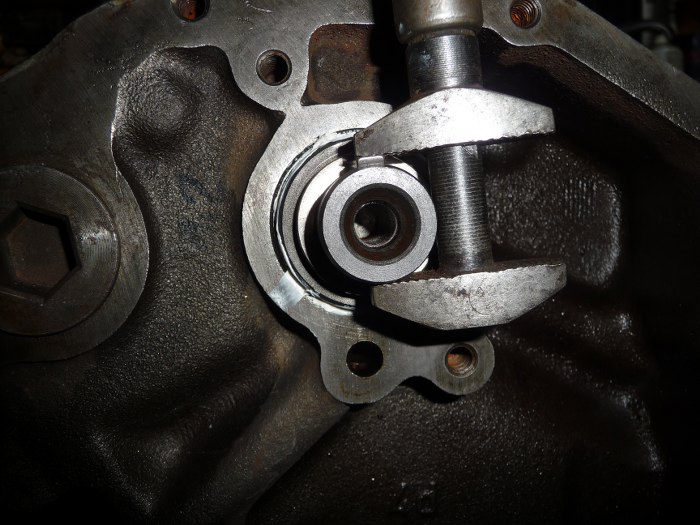
Potem mogłem już przykręcić płytkę mocującą wałek rozrządu do bloku. Do śrub warto tu użyć kleju do gwintów.
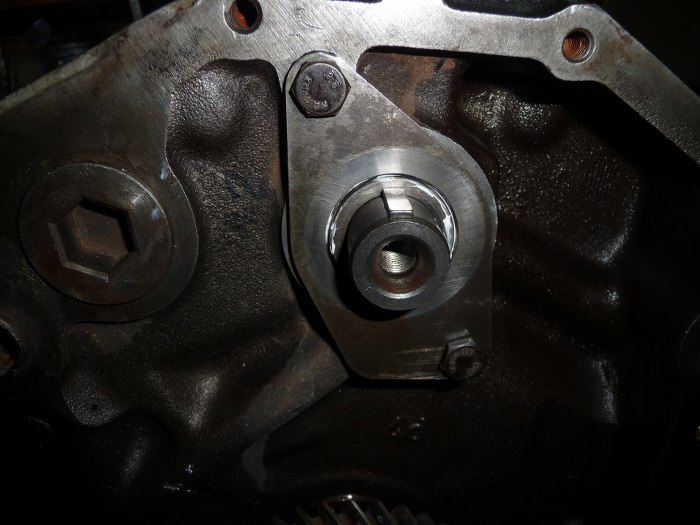
Teraz w tych silnikach nadchodzi moment, w którym trzeba mieć wszystko wcześniej przygotowane. Blacha, którą widać poniżej, jest przykręcana na dwie śruby do bloku. Pod nią jest uszczelka, którą, jak zawsze, lekko smaruję preparatem uszczelniającym. Zanim on wyschnie, trzeba poskładać wszystkie elementy składowe rozrządu. Aha, widzisz te dwa otwory w bloku, po jego obu stronach? To są kanały wodne, przechodzące przez pokrywę aż do pompy wody. Dookoła nich jeszcze przychodzą uszczelki.
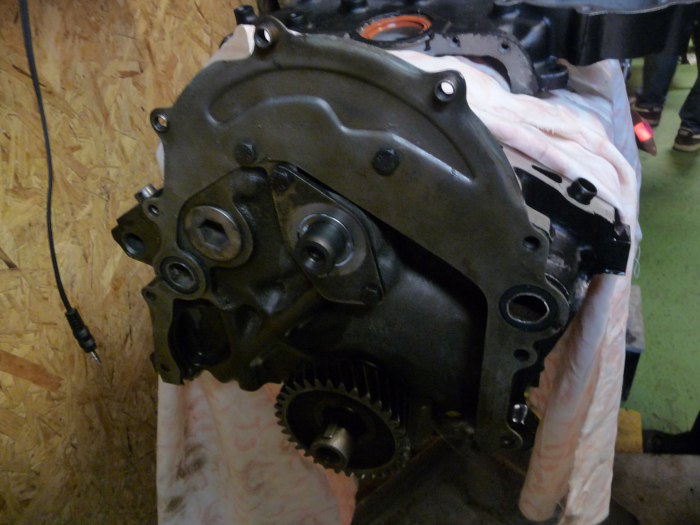
Nad blachę zakładam koło zębate wałka rozrządu, oczywiście ustawiając je odpowiednio, na znaki. Potem jest kolejna uszczelka i na nią zakładam pokrywę rozrządu. W niej musi być już wcześniej założony uszczelniacz przedniej części wału. Po dokręceniu pokrywy zazwyczaj wzdycham z ulgą :)
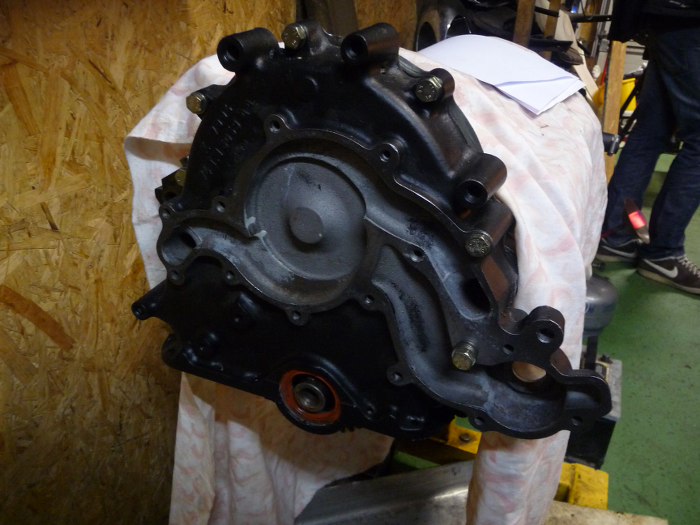
Następnie rozkręciłem pompę oleju i posmarowałem ją smarem montażowym. Dzięki temu przy pierwszym kręceniu pompą będzie łatwiej zasysała olej. Pompa oczywiście jest nowa.
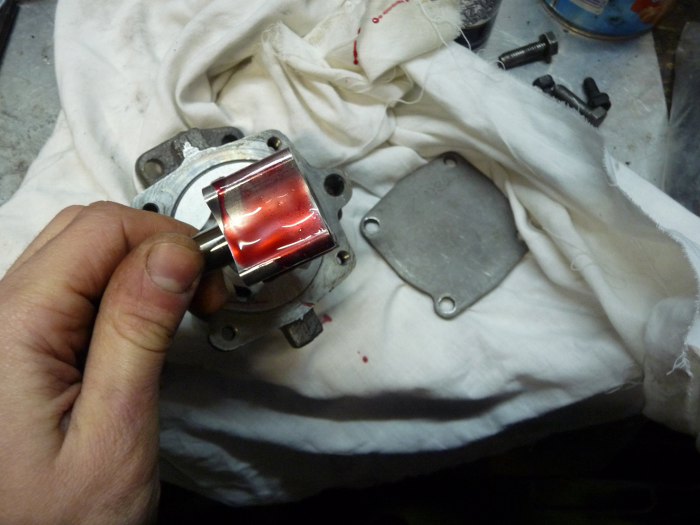
Potem pompę przykręciłem do bloku.
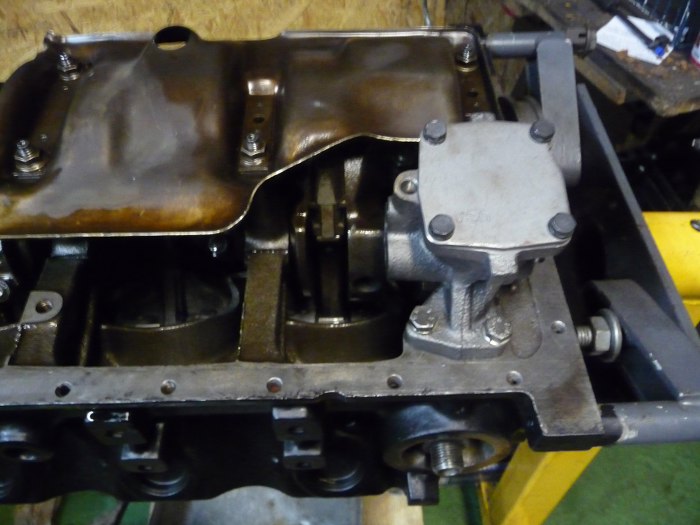
Tu nastąpił kolejny zonk - w moim silniku wszystko pasowało, bo i tą blachę, i pompę oleju miałem od coswortha. Tu pompa jest starszego typu i smok nie pasuje :( Dlatego niestety blachę musiałem pożegnać nieczule. Trochę szkoda.
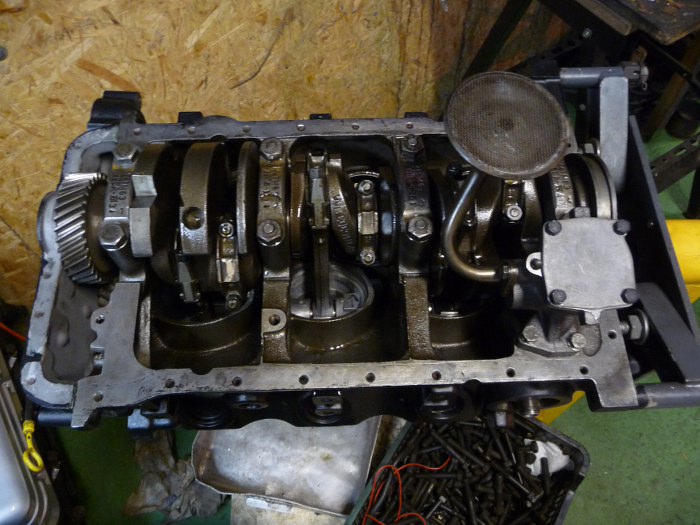
Koła rozrządu posmarowałem smarem montażowym. Po obu stronach, na łączeniu pokrywy z blokiem widać, że wyrównałem płaszczyzny łączenia. Ułatwi to przyleganie uszczelek miski olejowej.
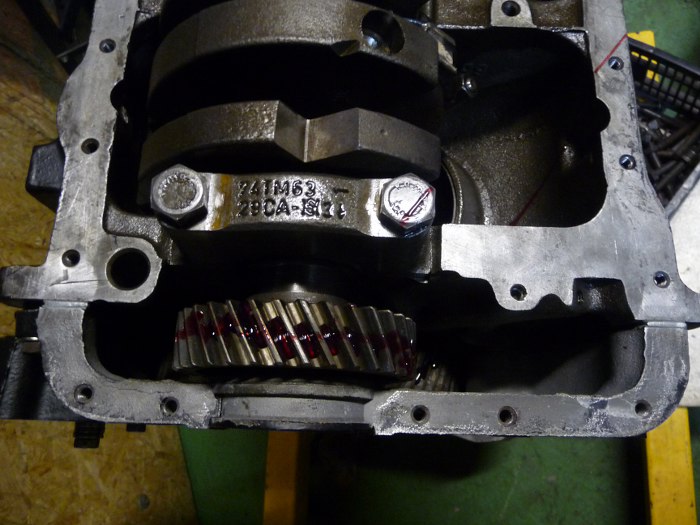
Następnie ułożyłem uszczelki i przykręciłem miskę olejową. Przypominam, że silnik buduję z prawie gołego bloku, cała reszta jest albo wygrzebana z szuflad garażu, albo dokupiona.Podobnie było z miską, a śrubki akurat prościej było użyć nowe niż szukać oryginalnych.
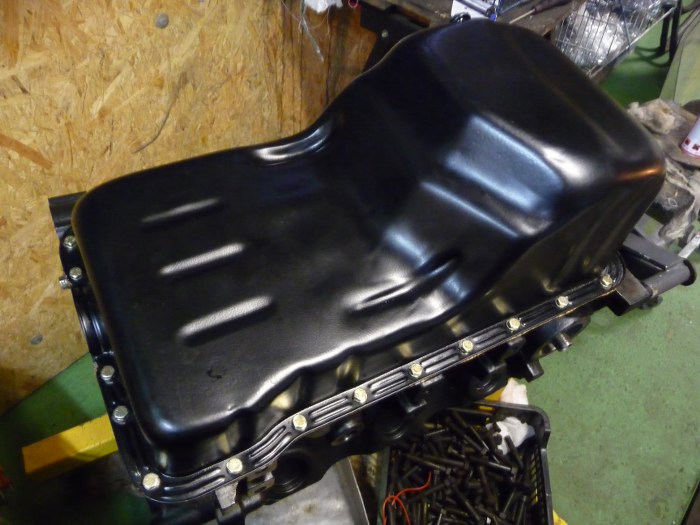
Następnie popychacze. Rybaak dostarczył komplet nowych, razem z wałkiem i sprężynami zaworowymi.
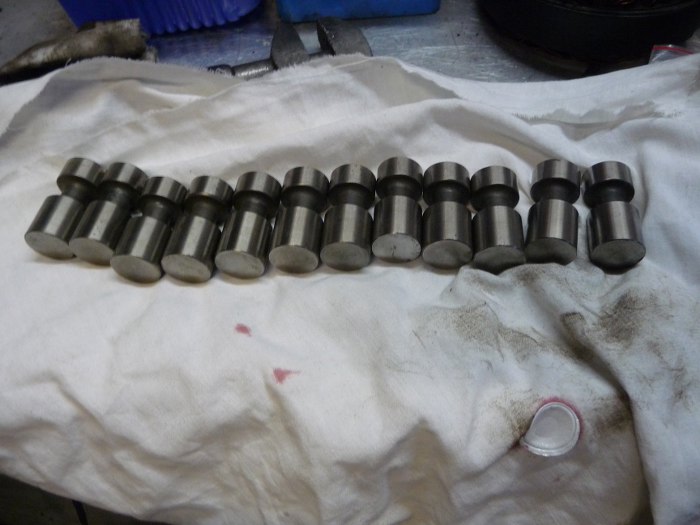
Po posmarowaniu gładzi olejem, popychacze powinny same powoli opaść pod własnym ciężarem. Wtedy wiemy, że wszystko będzie pracować poprawnie. Na szczęście w tych silnikach bardzo rzadko w tym miejscu coś się zużywa.
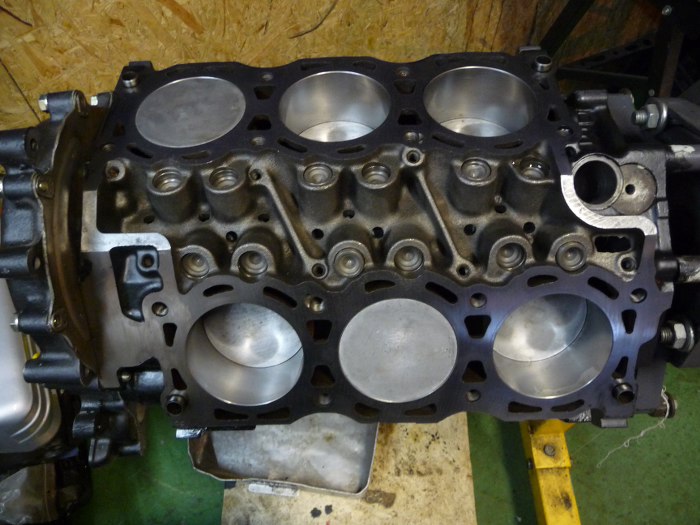
Następnie poskładałem zawory do jednej ze swoich starych głowic i przykręciłemją lekko do bloku. Poskładałem kompletny mechanizm rozrządu dla tego jednego cylindra, w którym były zawory i przekręciłem kilka razy wał. Wszystko to dla sprawdzenia, ile można splanować głowicę. DUŻO. Ale o tym później.
Okazało się, że znalazłem niechcący błąd w katalogach. Tłoki nadwymiarowe, które kupiłem, miały mniejszą wysokość kompresyjną (jest to odległość od osi sworznia tłoka do denka tłoka). Nadawałyby się idealnie pod turbo, ale niestety ten silnik nie będzie miał turbo :). Wysokość kompresyjna była mniejsza o ~2mm, co powodowałoby obniżenie stopnia sprężania. Nie podobało mi się to.
Próbowałem wymyślić kilka rozwiązań, jak np. planowanie bloku, wymiana wału korbowego na taki od 2.9 (ma większy skok)... niestety żaden z tych pomysłów nie sprawdziłby się w praktyce. Dlatego ze spuszczoną głową znalazłem w stercie swoich części tłoki nominalne w idealnym stanie (właściwie nowe), chomikowane na jakąś okazję kiedyś, a następnie oddałem blok do tulejowania cylindrów pod te nominalne tłoki.
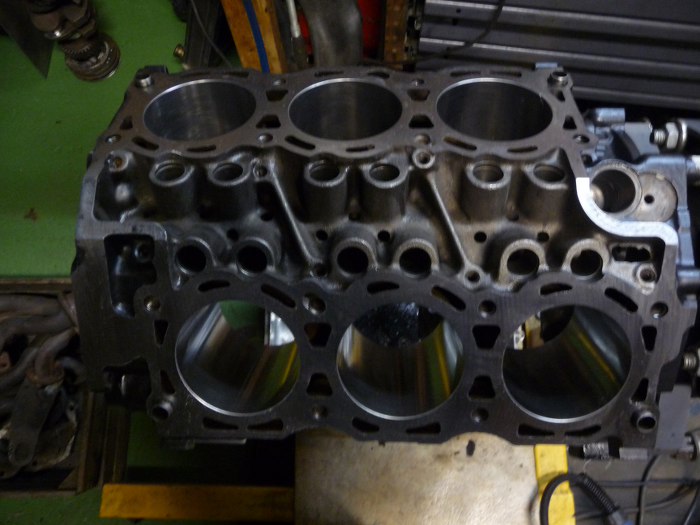
Wał został doważony pod tłoki, które będą teraz użyte. Po włożeniu panewek i posmarowaniu ich olejem położyłem wał korbowy na miejsce. Następnie założyłem uszczelniacz tylny wału - najłatwiej to zrobić w tym momencie.
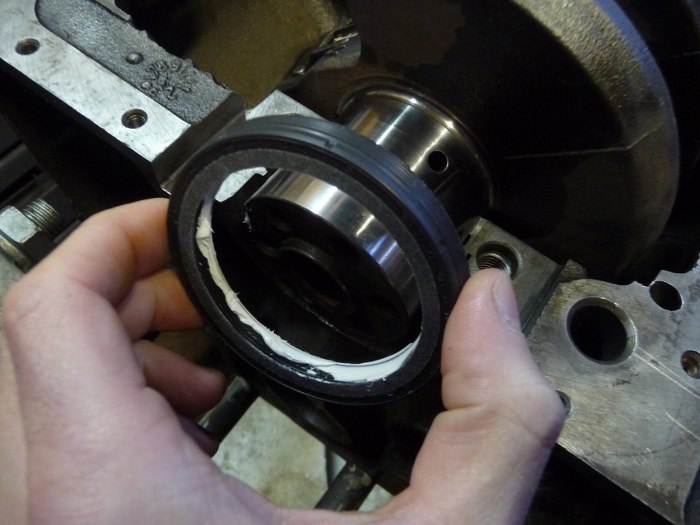
Gotowe do przykręcenia stóp wału.
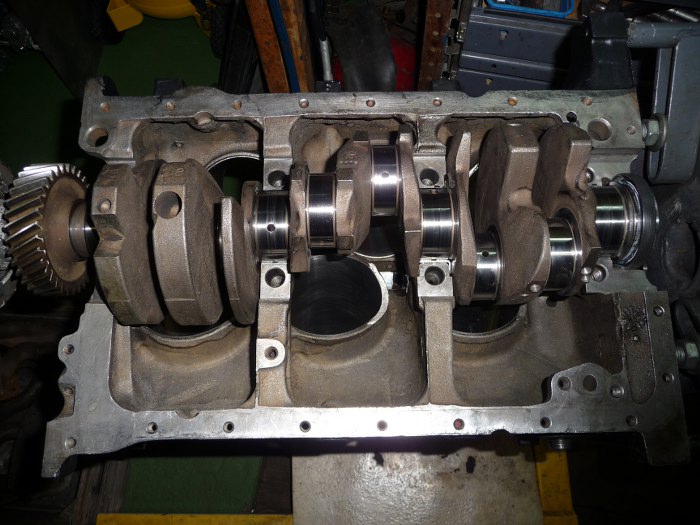
Musiałem jeszcze tylko przygotować czwartą śrubę pod blachę w misce olejowej.
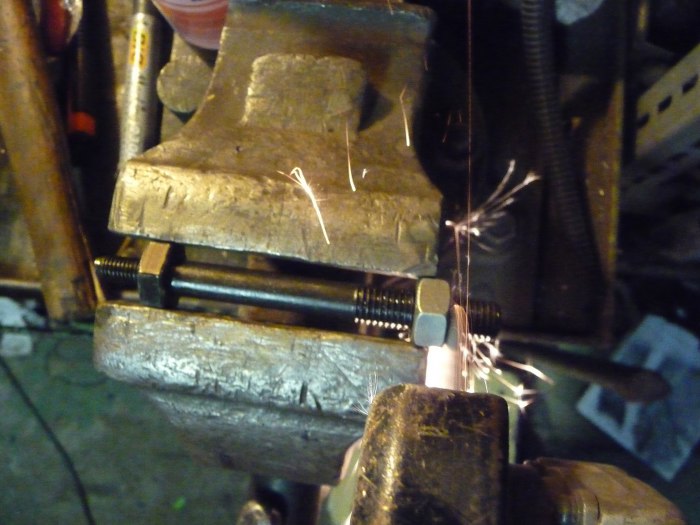
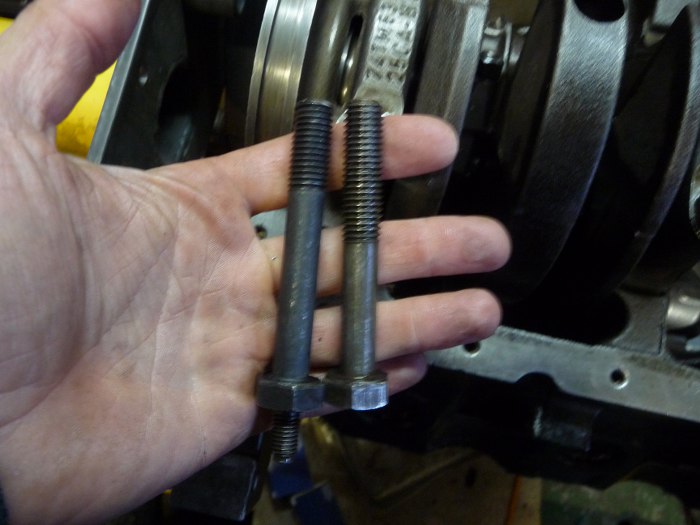
Przykręcone.
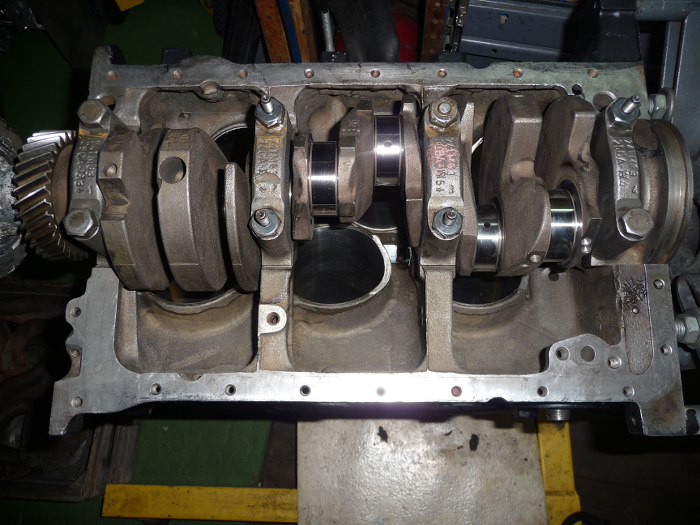
Następnie dokupiłem brakujące obecnie pierścienie. Poprzednie były do nadwymiarowych tłoków.
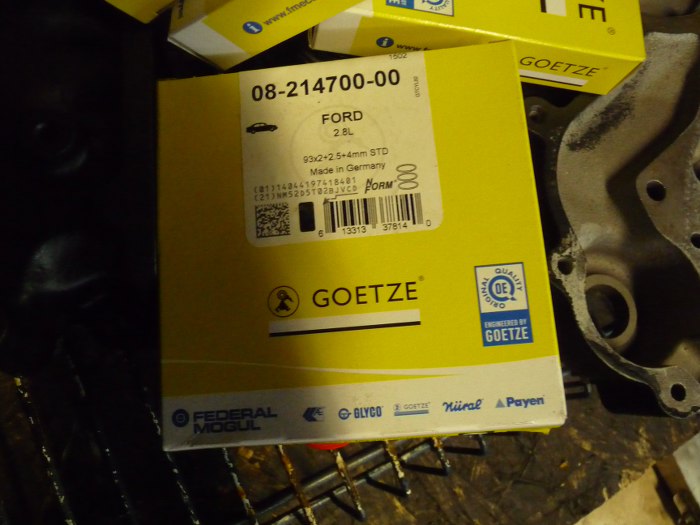
Wreszcie się nauczyłem korzystać z przyrządu do zakładania pierścieni! Jakoś nigdy do niego nie miałem serca, wolałem robić to ręcznie, ale już mnie palce od tych pierścieni bolały :)
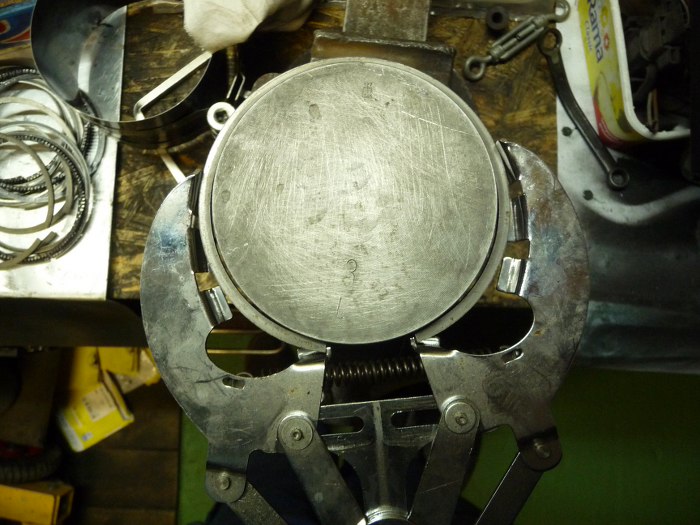
Następnie standardowo - ściśnięcie pierścieni i założenie osłonek na śruby korbowodu, żeby nie uszkodzić wału.
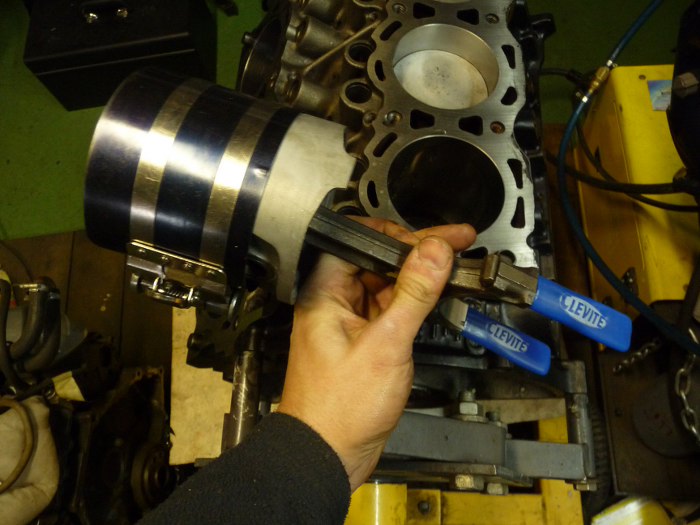
Po włożeniu każdego z tłoków warto zrobić z 2-3 obroty wałem korbowym, żeby sprawdzić, czy wszystko obraca się bez dziwnych oporów.
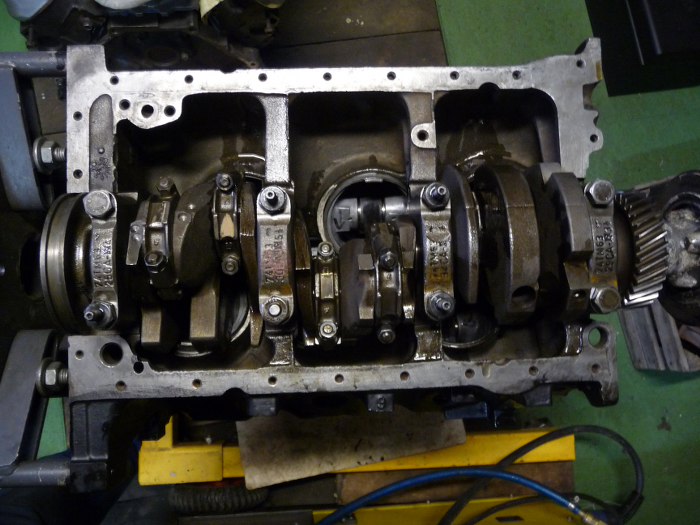
Następnie przykręciłem blachę na stopy wału.
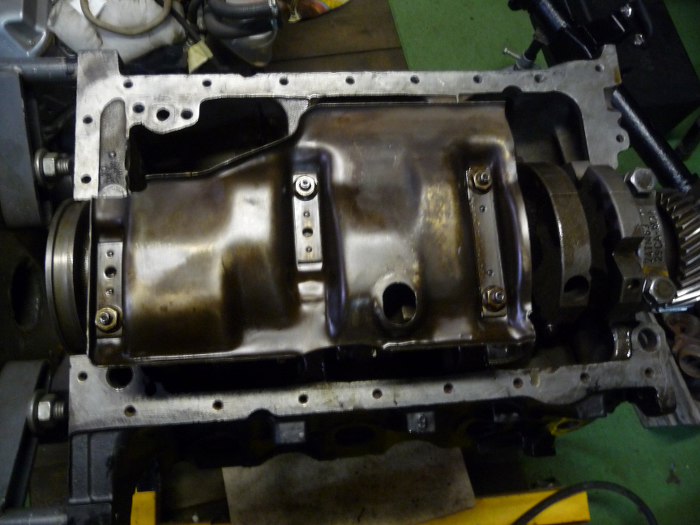
Tak to wygląda z góry. Teraz jest ok, bo tłok w górnym położeniu jest na równo z płaszczyzną bloku, a poprzednie tłoki były ~2mm poniżej tej płaszczyzny.
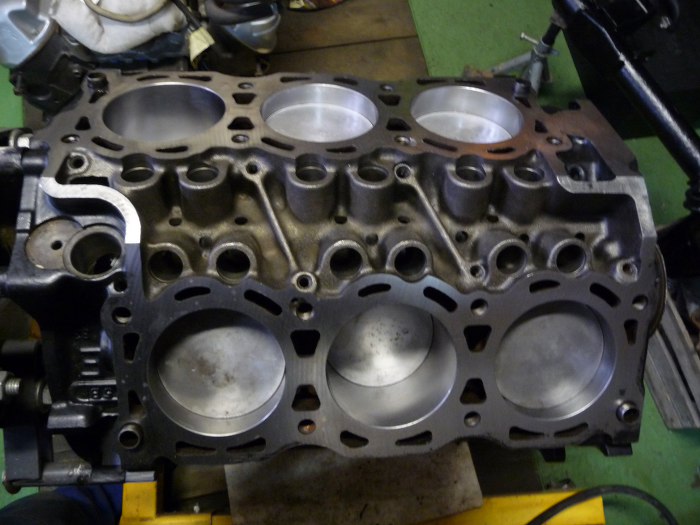
Następnie wziąłem się za to, na czym skończyłem poprzednią stronę - za szukanie brakujących elementów mocujących. Znalazłem 3 :)
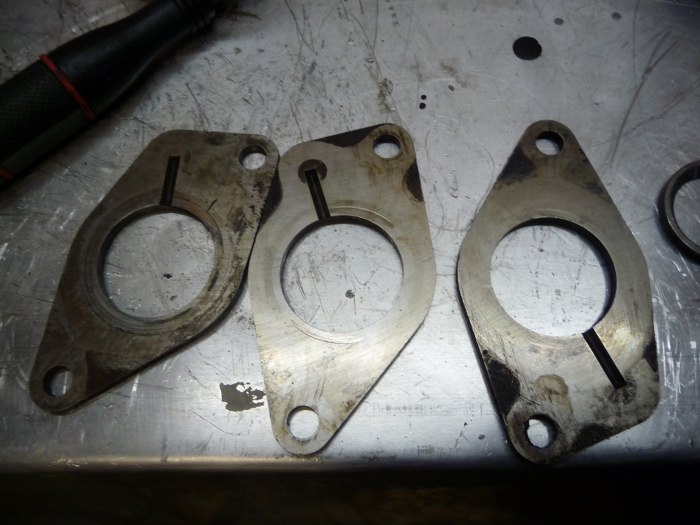
Po wybraniu najlepszego, poszukałem jeszcze śrub, klina i podkładki dystansowej.
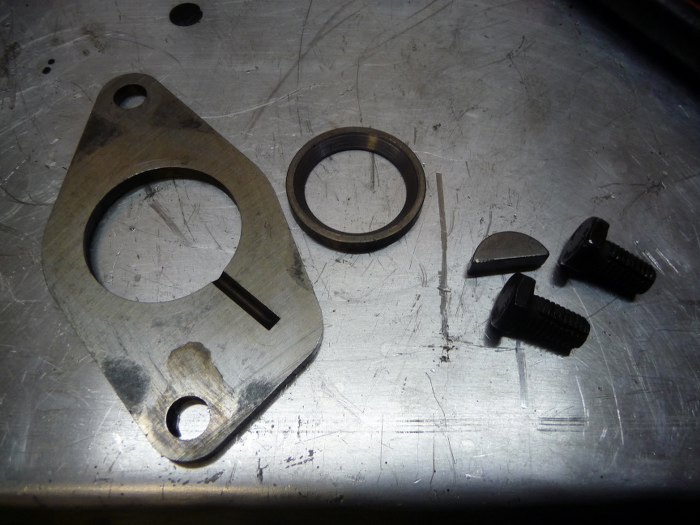
Podkładkę trzeba założyć podtoczoną stroną w kierunku wałka rozrządu.
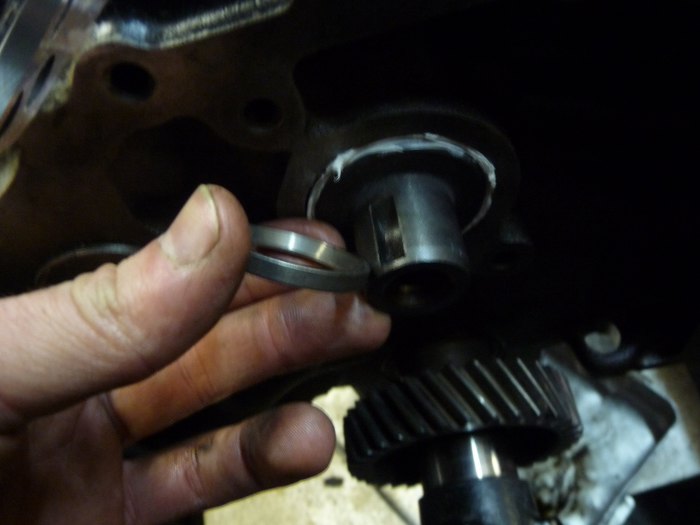
Następnie musiałem wykombinować jak wcisnąć klin w wałek. Stanęło na kluczu francuskim.
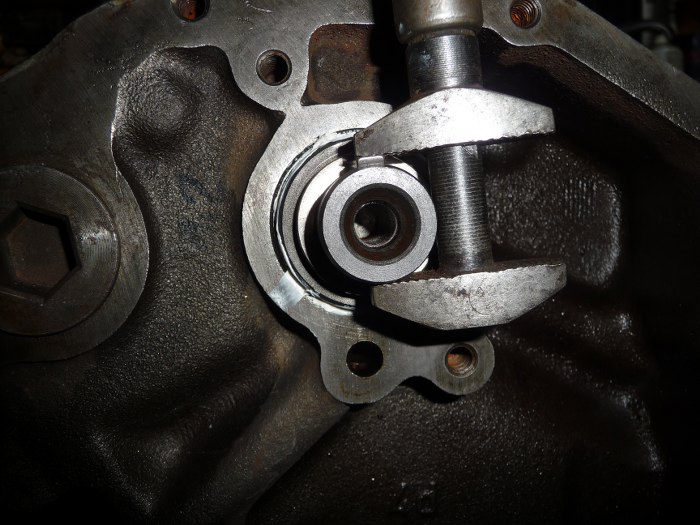
Potem mogłem już przykręcić płytkę mocującą wałek rozrządu do bloku. Do śrub warto tu użyć kleju do gwintów.
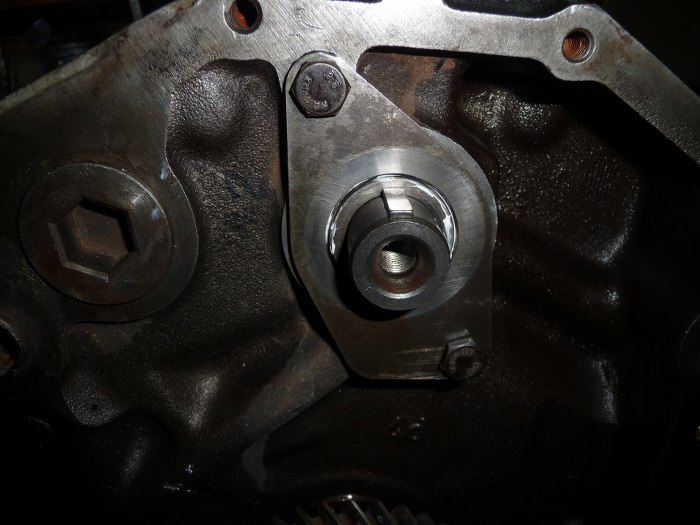
Teraz w tych silnikach nadchodzi moment, w którym trzeba mieć wszystko wcześniej przygotowane. Blacha, którą widać poniżej, jest przykręcana na dwie śruby do bloku. Pod nią jest uszczelka, którą, jak zawsze, lekko smaruję preparatem uszczelniającym. Zanim on wyschnie, trzeba poskładać wszystkie elementy składowe rozrządu. Aha, widzisz te dwa otwory w bloku, po jego obu stronach? To są kanały wodne, przechodzące przez pokrywę aż do pompy wody. Dookoła nich jeszcze przychodzą uszczelki.
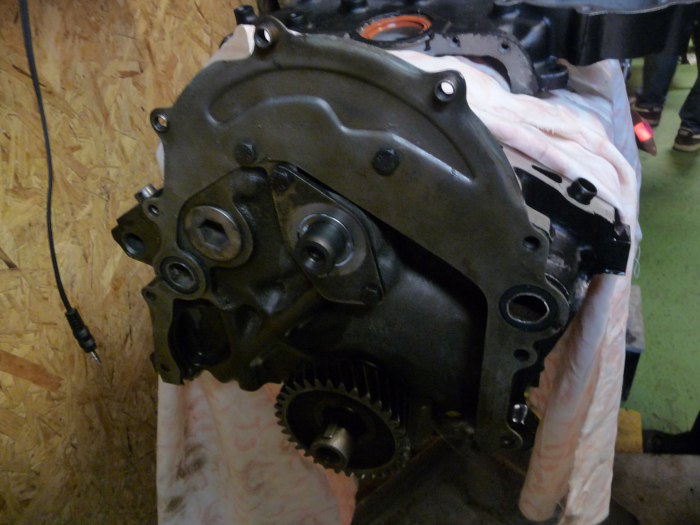
Nad blachę zakładam koło zębate wałka rozrządu, oczywiście ustawiając je odpowiednio, na znaki. Potem jest kolejna uszczelka i na nią zakładam pokrywę rozrządu. W niej musi być już wcześniej założony uszczelniacz przedniej części wału. Po dokręceniu pokrywy zazwyczaj wzdycham z ulgą :)
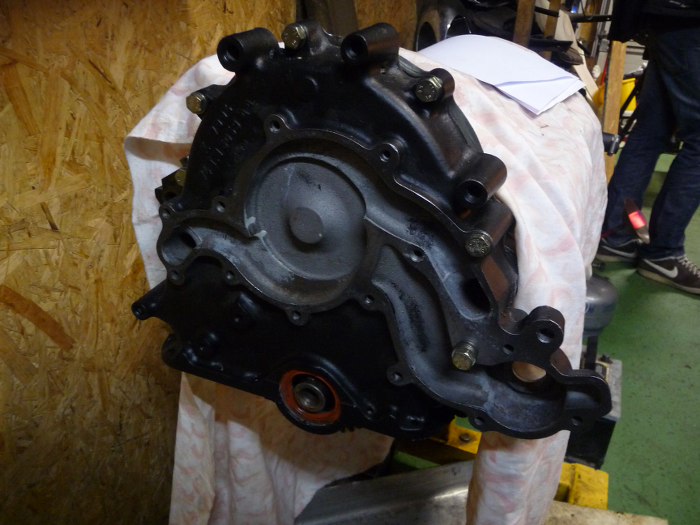
Następnie rozkręciłem pompę oleju i posmarowałem ją smarem montażowym. Dzięki temu przy pierwszym kręceniu pompą będzie łatwiej zasysała olej. Pompa oczywiście jest nowa.
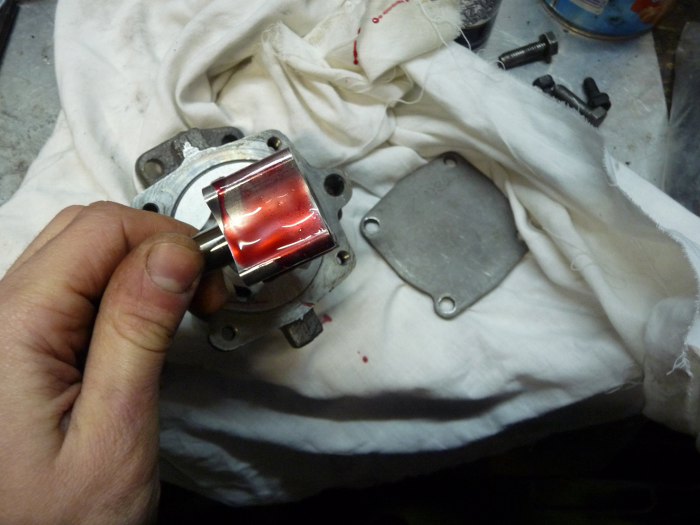
Potem pompę przykręciłem do bloku.
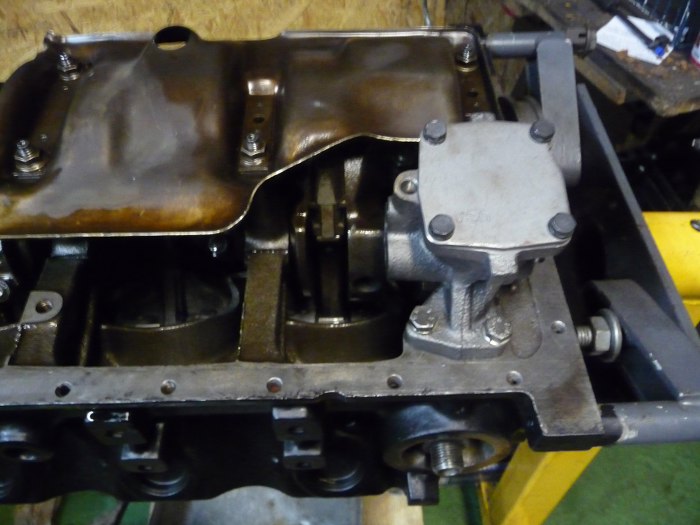
Tu nastąpił kolejny zonk - w moim silniku wszystko pasowało, bo i tą blachę, i pompę oleju miałem od coswortha. Tu pompa jest starszego typu i smok nie pasuje :( Dlatego niestety blachę musiałem pożegnać nieczule. Trochę szkoda.
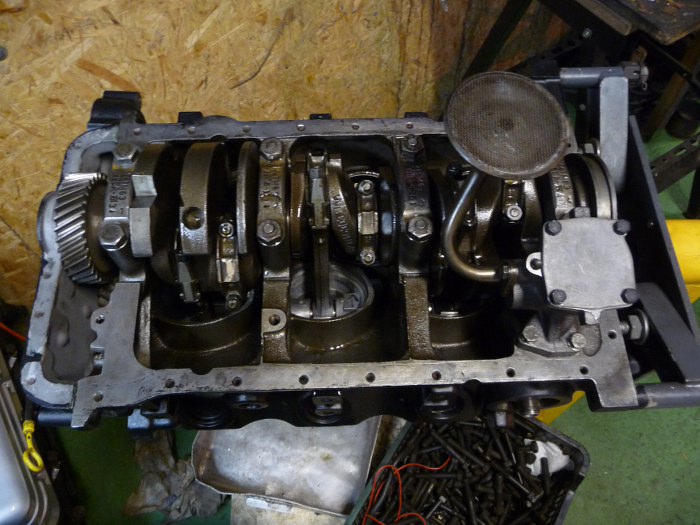
Koła rozrządu posmarowałem smarem montażowym. Po obu stronach, na łączeniu pokrywy z blokiem widać, że wyrównałem płaszczyzny łączenia. Ułatwi to przyleganie uszczelek miski olejowej.
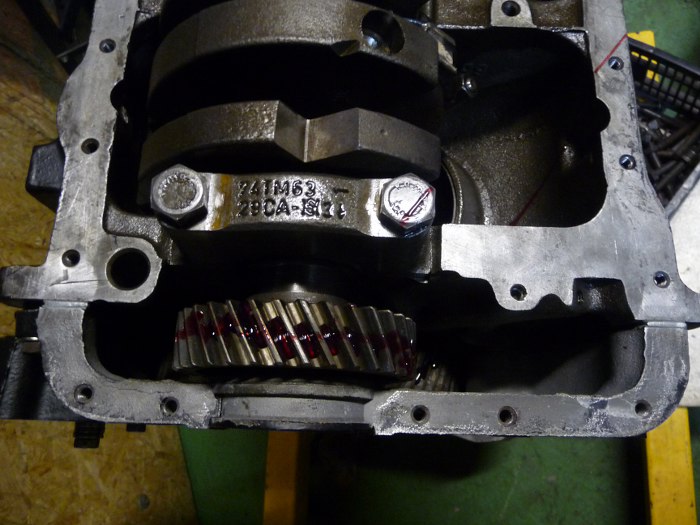
Następnie ułożyłem uszczelki i przykręciłem miskę olejową. Przypominam, że silnik buduję z prawie gołego bloku, cała reszta jest albo wygrzebana z szuflad garażu, albo dokupiona.Podobnie było z miską, a śrubki akurat prościej było użyć nowe niż szukać oryginalnych.
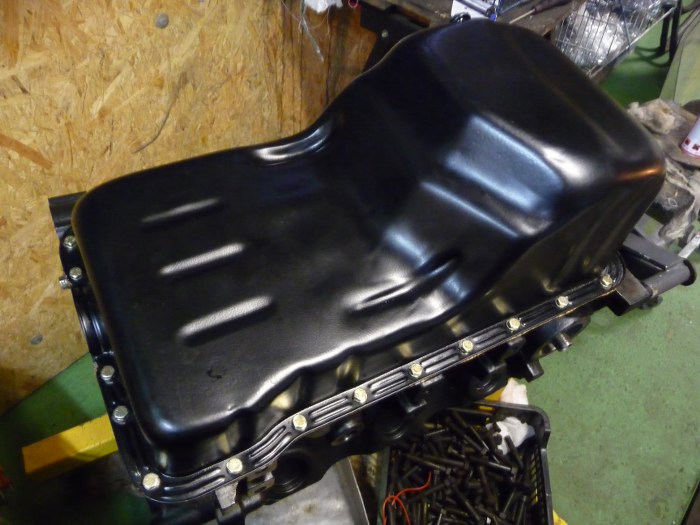
Następnie popychacze. Rybaak dostarczył komplet nowych, razem z wałkiem i sprężynami zaworowymi.
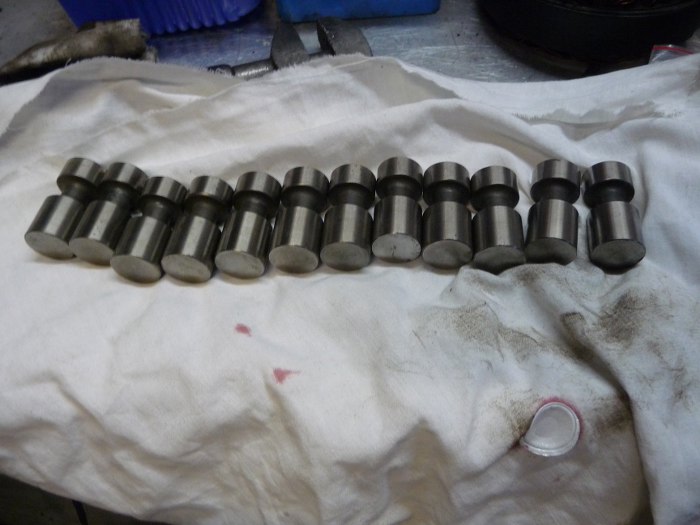
Po posmarowaniu gładzi olejem, popychacze powinny same powoli opaść pod własnym ciężarem. Wtedy wiemy, że wszystko będzie pracować poprawnie. Na szczęście w tych silnikach bardzo rzadko w tym miejscu coś się zużywa.
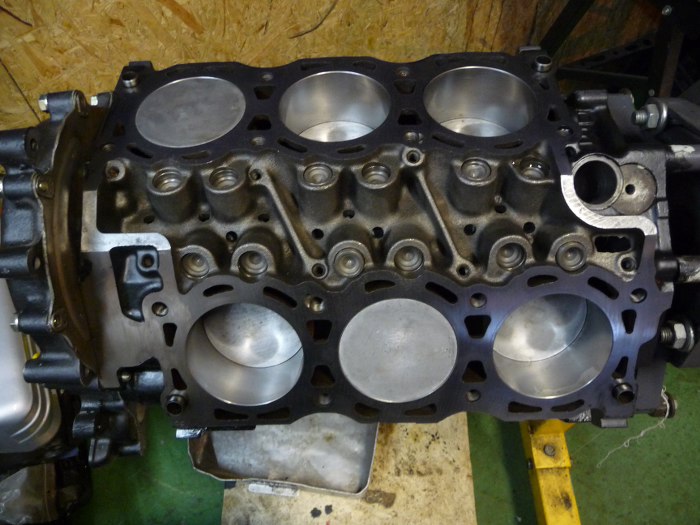
Następnie poskładałem zawory do jednej ze swoich starych głowic i przykręciłemją lekko do bloku. Poskładałem kompletny mechanizm rozrządu dla tego jednego cylindra, w którym były zawory i przekręciłem kilka razy wał. Wszystko to dla sprawdzenia, ile można splanować głowicę. DUŻO. Ale o tym później.